Do you know how THY Precision Injection Molding Machine Types are changing the future of making things? The plastics industry is getting bigger, with a market expected to hit 750.1 billion U.S. dollars by 2028. It’s vital to see how these machines are changing modern manufacturing.
Key Takeaways
- The plastics industry is the third largest manufacturing industry worldwide, with Injection Molding Machine Types contributing 80% of production.
- Industry 4.0 is transforming the value chain of industrial producers, and Injection Molding Machine Types are at the forefront of this revolution.
- Inline and real-time quality control of injection molded parts is a key requirement, defining injection molds as cyber-physical systems.
- The integration of machine learning and smart adaptive control is crucial for optimizing the Injection Molding Machine Types process.
- Understanding the role of Injection Molding Machine Types is essential for manufacturers to stay competitive in the digital age.
Injection Molding Machine Types and Early Industry 4.0 Efforts
The journey to Industry 4.0 started long ago, and Injection Molding Machine Types were key. In 1986, at the K trade fair, Arburg showed a fully automated system. It had injection molding machines connected under one computer, starting the “Computer-Integrated Manufacturing” (CIM) era.
Computer-Integrated Manufacturing: A Precursor to Industry 4.0
This CIM system showed how injection molding machine types could work together with other machines. Over the years, the plastics industry has seen huge improvements in technology. This has made it possible for more complex processes to meet the demand for more production.
Putting Industry 4.0 to Work with InjectionMoldingMachineTypes
Now, the most forward-thinking molders are using Industry 4.0 tech. They connect injection molding machines, robots, and computers to make their processes better. This makes their operations more reliable, efficient, and valuable. The key is in how well machines talk to each other, changing how plastic Injection Molding Machine Types work.
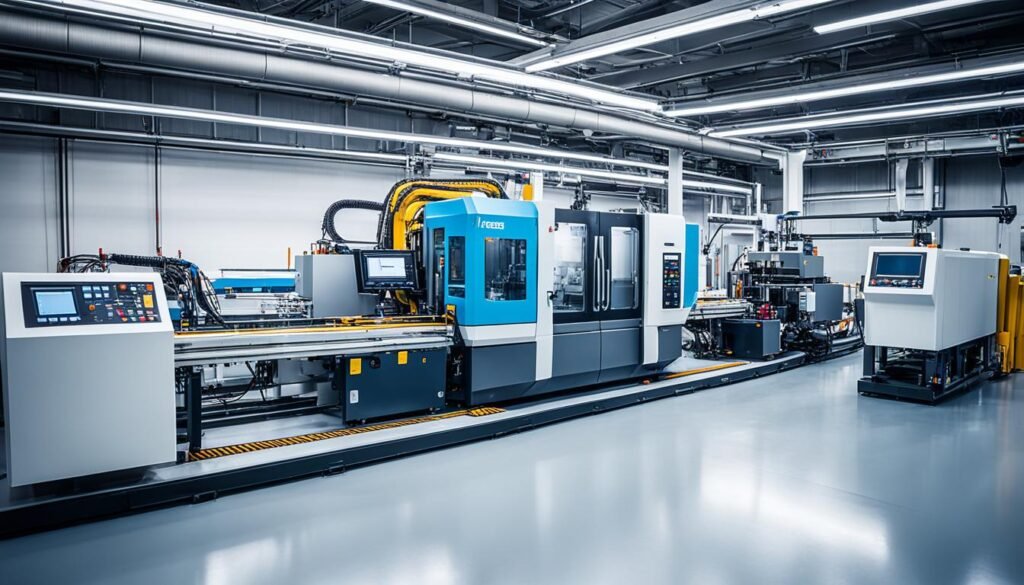
“The most innovative molders are already embracing the transformative power of Industry 4.0 technologies.”
Injection Molding Machine Types: Key Enablers of Industry 4.0
The shift to Industry 4.0 has made injection molding machine types more important. These plastic injection molding machines lead the way in combining automation, data sharing, and smart manufacturing. They are key to this new era.
Today, injection molding machinery is more than just a tool for making products. It’s a smart system that can adapt to the fast-paced needs of Industry 4.0. These types of injection molding machines have features that help drive this change:
- Enhanced process control and monitoring: Injection molding machine types now have advanced sensors and control systems. They provide real-time data on important process parameters. This lets for precise adjustments and optimization.
- Connectivity and data integration: Injection molding machines connect to wider IT networks. This lets them collect and analyze “big data”. This data helps in making informed decisions and predictive maintenance.
- Adaptive automation: Plastic injection molding machines can change their settings and operations on their own. They do this based on the changing production needs. This makes them more efficient and flexible.
- Intelligent assistance features: Types of injection molding machines come with easy-to-use interfaces and smart help functions. These reduce the need for special knowledge. They make it easier for operators to handle complex tasks.
By using these advanced injection molding machine types, manufacturers can easily move to Industry 4.0. This brings new levels of productivity, quality, and the ability to quickly respond to market changes. As the industry keeps evolving, these injection molding machines will lead the way in smart manufacturing.
Feature | Benefit |
---|---|
Enhanced process control and monitoring | Precise adjustments and optimization of critical parameters for improved product quality and consistency |
Connectivity and data integration | Enables data-driven decision-making and predictive maintenance for enhanced operational efficiency |
Adaptive automation | Increased flexibility and responsiveness to changing production demands for improved profitability |
Intelligent assistance features | Reduced need for specialized knowledge and empowerment of operators for streamlined production processes |
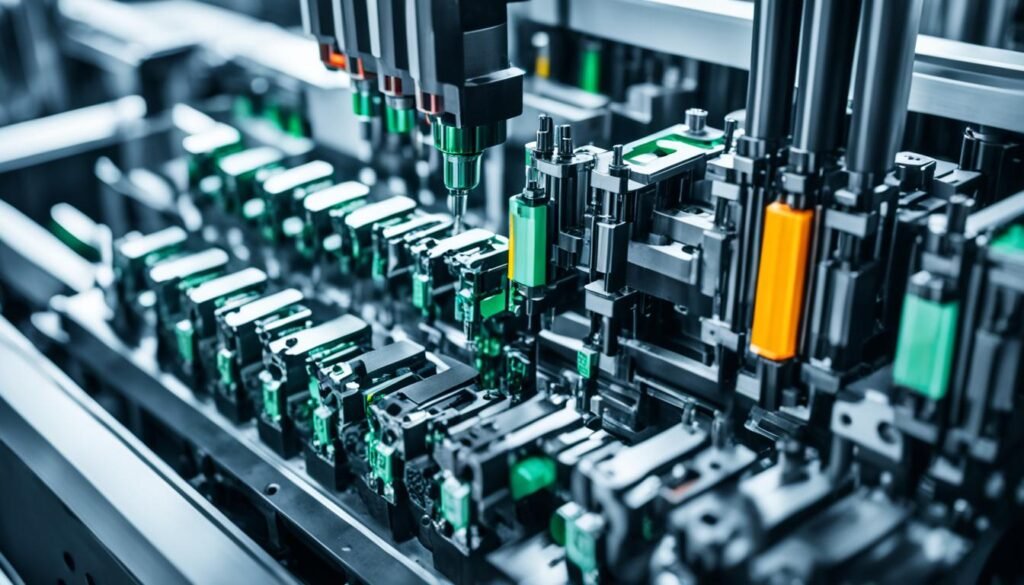
“The future of manufacturing lies in the seamless integration of advanced injection molding machine types with the broader ecosystem of Industry 4.0. These intelligent systems are the key to unlocking new levels of productivity, quality, and agility.”
– THY Precision, Industry Thought Leader
Networking and Data Management for Injection Molding Machine Types
The injection molding industry is moving into Industry 4.0. This change highlights the need for better IT networking and data management. THY Precision leads in offering injection molding machine types. They know how crucial it is to link production systems with detailed data collection.
IT Networking and ‘Big Data’ Collection
At the core of this change is a strong manufacturing execution system (MES) linked to the company network. This setup lets THY Precision’s customers gather, process, analyze, and store all important data. By using big data, molders can make their production better, work more efficiently, and make smart decisions that lead to new ideas.
Standard Interface for Data Exchange
THY Precision is working with other top injection molding machine types makers and software creators on the Euromap 77 standard. This standard makes it easier to share data between machines and the MES. It lets the host computer start a job in the machine, and the machine sends back job details to the host.
By combining IT networking and data management, THY Precision helps its customers fully use Industry 4.0. This leads to better efficiency, quality, and flexibility in their injection molding machine types work.
“The key to efficient regulation and control of machines, automation, and the entire manufacturing process from an Industry 4.0 perspective is the IT networking of production with a high-performance manufacturing execution system (MES) that is directly connected to a company network.”
Conclusion
The industry is changing fast, making it key to use injection molding machines with Industry 4.0 tech. THY Precision leads in making advanced machines for smart manufacturing.
By linking your machines with Industry 4.0 tech, you get huge gains in making things faster, better, and with less downtime. Features like smart management systems and automated adjustments help you run your molding operations smoothly.
With real-time data, you can keep your products top-notch and keep up production, even when you can’t get help from machine makers. Using Industry 4.0, your machines help lead your smart manufacturing efforts. This puts your business ahead in a changing market.